If you decide, as I did, that P-static presents a risk to radio
reception and possibly to the integrity of the moving joints of the
aircraft's control surfaces, then you'll want to install static wicks
and bonding straps. This page covers the installation requires for
static wicks on the rudder of the RV-10. You'll also want them on the
elevators, wingtips, and ailerons—but that will be covered
separately when I get to those stages.
The assembly sequence described here
requires that you install
some extra hardware before riveting the two sides of the rudder
together. I did this installation immediately before buttoning up the
rudder and after priming, so that the new holes I drilled would have the
best eletrical conductivity when riveted together.
Parts Selection
I selected the Dayton-Granger 16165 static wick part for a couple of
reasons. First, they seem to be highly regarded by reviewers on the
internet. Second, D-G has published a document showing exactly where
and how many of the 16165 wicks are required for the RV-10:
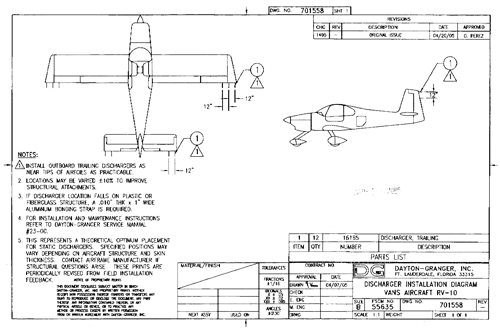
For the rudder, they recommend two wicks. One as close to the top end
of the trailing edge as possible, and one twelve inches below that. The
16165 wicks aren't the cheapest; I was able to get them for $42 each at
skygeek.com. The recommended loadout for the RV-10 is twelve wicks
total, so you're looking at over $500 just for wick hardware. Half go on
the empennage and half on the wings, so if you think of it as two $250
purchases separated by quite some time, it's a bit easier to swallow.
I wanted my static wicks to be removable, either for aesthetic reasons
when showing off the plane with clean lines, or for replacement if the
wicks wear out. Thus, I decided to use screws and locking anchor nuts
rather than the usual blind rivet solution. Besides, the holes in the
wicks are much too large for any blind rivets I've seen. The holes in
the wicks are sized for #10 hardware, so AN515-10 washer-head screws
seem like a natural match. For reasons I'll go into in the assembly
section, below, the AN515-10R6 is the correct length to get.
A good elastic-insert anchor nut for #10-32
hardware is the AN366F-1032A which I bought from Aircraft Spruce. In order to
take advantage of the extremely low headroom environment inside the
trailing edge of the rudder, I bought some MS21080-3 one-lug elastic-insert
anchor nuts as well for the aft-most screws.
Assembly
The D-G installation diagram for the RV-10 indicates that the top rudder
wick should be as close to the top of the trailing edge as possible, and
that the lower one should be twelve inches away. It allows for a 10%
change in these locations in order to take advantage of the
availability of structural mounting positions.
In the RV-10, the
underlying stiffeners are almost perfectly suited for the D-G
recommendations. The top fairing contributes essentially zero height to
the trailing edge, so the top rib's aft-most point is right at the
top of the trailing edge. This rib makes a perfect location for the
upper wick's attachment hardware.
The second stiffener down from the top is almost exactly 12" below the
top rib, and thus it makes an excellent choice for a built-in structural
reinforcement for the lower rudder wick.
Since both wicks locations have built-in doublers already, nothing more
is required beyond the screws, anchor nuts, a few rivets, and the wick
itself. Here is a picture of the anchor nuts sitting in place on the
inside surface of the upper rib:
In this position, there is just enough headroom for the aft anchor nut,
so the screw has to be sized just right so as not to protrude from the
elastic side of the nut when tightened down. The AN515-10R6 is perfect
for this. Here is a side view showing how little clearance there is:
Note, however, that both of these pictures were taken with the hardware
resting on the right-side skin. In practice, it makes a lot more sense
to add the wicks to the left-side skin so that they add a bit to the
generally-desireable right rudder effect. I used the right-side skins
for testing the anchor nut head room because the stiffener was slightly
taller on this side and was a better estimator of the total space
available between the skins.
Once the locations for the rivet and screw holes are determined, I
recommend making a hole template out of scrap sheet aluminum for the
anchor nut hole pattern, then using that to drill the holes in the
rudder skin and stiffeners. I didn't do this the first time through and
the holes were a bit wonky as a result. Here are the holes for the
lower of the two wicks:
And here is the same spot, from the other side, after the anchor nuts
were installed:
Note that the rivets for the anchor nuts must be flush or the wick
hardware can't sit flat against the skin. Also, the anchor nuts won't
accept a dimpled hole. Thus, the skin/stiffener combo must be machine
countersunk to accept the rivet. Because of the weird angle of the
stiffener beneath the skin, I was not able to do this with my drill
press and ended up doing it manually with my deburring tool and
countersinking bit, one turn at a time and testing the fit of the rivet.
In the end, I got great results. Once this is done for both locations, the wicks themselves can be
screwed on for a test.
Once I had confirmed that I was happy with the installation, I
removed the wicks and screws and set them aside for the duration of
the RV-10 construction project. Won't need to install them again
until the plane is ready to fly.